Artikel
5 Vital Distribution Centre Processes and Benefits Explained
What Is a Distribution Centre? Key Processes and Benefits Explained
In the modern e-commerce landscape, a business needs more than just inventory storage to thrive. That is why many companies are turning away from traditional warehouses and leveraging technology, expertise and strategies to take their logistics operations up a notch by providing distribution centres.
These centres provide efficient supply chains that can ensure products move quickly into consumers’ hands.
In this article, we will take a closer look at what distribution centres are and cover their benefits and key processes.
Wichtige Punkte
- Distribution centres function as hubs for order fulfilment by providing efficient and effective storage of goods before shipping out, as well as value-added services.
- Despite people often using the terms "distribution centre" and “warehouse” interchangeably, it's important to realise that these two often overlap but differ in many aspects of their operations.
- There are five distribution centre processes that work in tandem for a timely and effective fulfilment of your customers’ needs.
- There are several benefits that modern distribution centres can offer e-commerce stores that wish to improve and expand their operations.
What Is a Distribution Centre?
Distribution centres are a pivotal part of the supply chain, providing an efficient and effective way to store goods before they ship out. Acting as hubs for order fulfilment – with potentially value-added services – these powerful state-of-the-art warehouse distribution centres help keep products flowing from supplier to customer quickly and cost-efficiently.
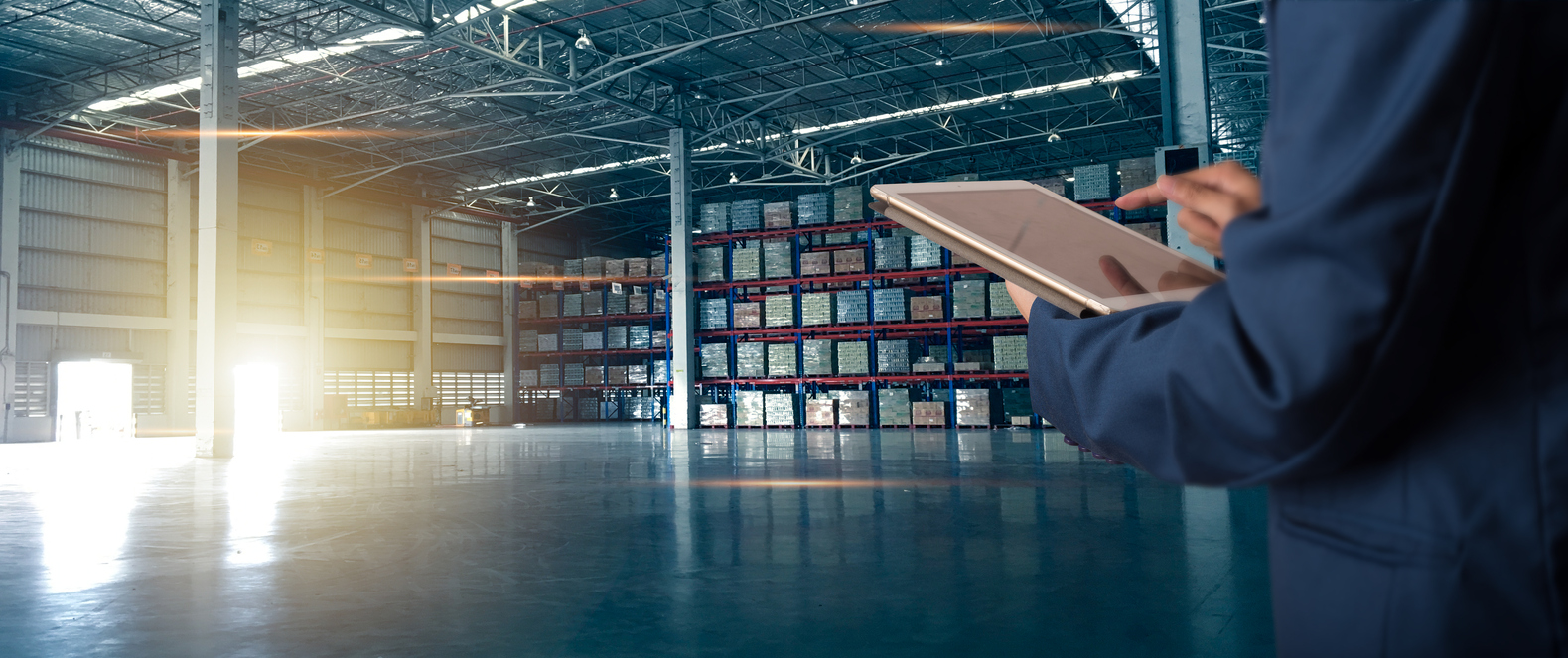
The Difference between a Warehouse vs Distribution Centre
Although it is common to believe that the terms “distribution centre” and “warehouse” are interchangeable, they have some key differences. A warehouse typically stores inventory over a long period of time, while a distribution centre provides brief storage for items until orders can be fulfilled and shipped off to their next or final destination.
Let’s look at what sets them apart so you can make an informed decision about which works best for your business:
1. More Customer-Centric Supply Chains
By shifting from warehouse storage to distribution centres, businesses are making their supply chains more customer-centric.
Distribution centres are the ideal solution for e-commerce businesses looking to maximise their logistics management. With a range of value-added services, distribution centres understand that customers come first and strive to deliver an unbeatable customer experience.
E-commerce businesses can gain access to comprehensive supply chain solutions with the help of a third-party logistics (3PL) provider such as Bezos.ai.
This customer-centric approach is designed to streamline inbound and outbound logistics, from receiving inventory to shipping orders directly to consumers while offering value-added services. These services include packing for an optimal unboxing experience, managing returns or even customising orders quickly and efficiently – resulting in significant savings in both time and cost.
2. Better Storage Management
When comparing warehousing and distribution centres, the latter offers improved storage management. With distribution centre storage management, retailers have access to cost-effective yet flexible options that provide efficient inventory solutions tailored specifically to their needs.
Distribution centres provide a critical service for businesses that require fast, reliable delivery of their products. Rather than relying on an in-house warehouse setup to store inventory and package orders, these facilities are managed by 3PL companies who specialise in speedily dispatching customer items with utmost efficiency. 3PL fulfilment centres facilitate the fulfilment process so consumers can enjoy swift order arrivals without sacrificing quality or reliability.
3. Streamlined In-House Processes
Warehouses are generally efficient for storage purposes; however, their lack of in-house processes limits opportunities to optimise the retail supply chain. With the power of automation and technological advancements behind us, warehouses have a significant potential to help stores cut costs and streamline operations – not just through simple space billing but also with innovative strategies based on industry standards.
Distribution centres are well-equipped to offer comprehensive solutions for businesses seeking ways to optimise their retail supply chain. With the implementation of technology, automation and best practices like order accuracy and speed optimisation, distribution facility centres have become a dependable asset in successfully streamlining an e-commerce fulfilment process while maximising cost savings potential.
Third-party logistics (3PL) providers offer a valuable service to online stores and shoppers alike. By utilising their technology, businesses are able to automatically send orders directly from their e-commerce platform to the closest distribution centre’s Warehouse Management System (WMS).
WMS system software gives businesses visibility into their complete inventory and handles the fulfilment of supply chain operations, from the distribution centre to store shelves.
Here orders are promptly picked, packed, and shipped out by an expert fulfilment team. Streamlining this key process helps bring customers closer than ever before with rapid delivery of goods combined with hassle-free retail experiences.
4. Expert Shipping Workflows
When using a warehouse, you have to ensure your stock reaches its destination quickly and efficiently. In order to do this, consider researching shipping solutions or services before delivery leaves the warehouse.
Distribution centres are the expert solution to timely shipping. By partnering with major carriers, they ensure that orders are quickly fulfilled and shipped out daily so customers can receive their goods swiftly.
Get your products to customers faster and for less money with a tech-enabled 3PL provider like Bezos.ai. Our streamlined approach eliminates manual processes, providing direct integrations between e-commerce platforms and fulfilment centres that automatically send customer orders straight through to the nearest distribution centre – ensuring efficient picking, packing and shipping. And once they’re on their way, order tracking info is seamlessly delivered back in real-time, so both you (and your customers) know where those items are at all times.
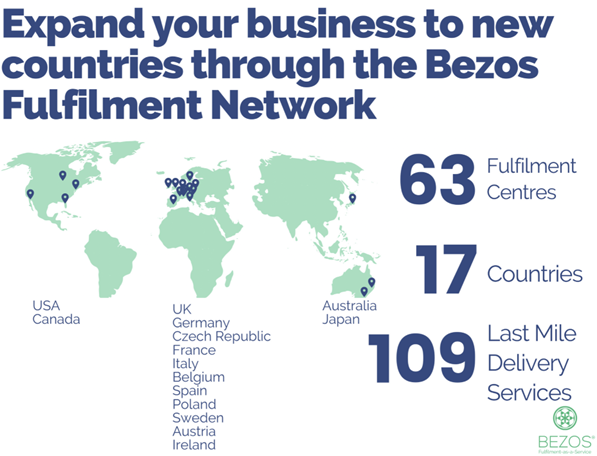
The 5 Crucial Distribution Centre Processes
To ensure quick and efficient delivery of orders, distribution centres are equipped with essential processes such as order picking, packing and shipping. Utilising these procedures allows for the most effective fulfilment of your customers’ needs in a timely manner.
1. Inventory Management
A key component of the distribution centre process is inventory management, which involves the tracking and monitoring of stock levels and orders to ensure that goods are available when they are needed. This process helps to reduce errors and minimise disruptions in supply chain operations. It also plays an important part in maintaining accurate product information and pricing.
2. Picking & Packaging
The picking and packaging process is another essential element of a distribution centre’s operation. Here, orders are selected from storage shelves, checked for accuracy against customer requirements, packed into boxes or other suitable containers and prepared for shipping. Automated systems may be employed in this process to increase efficiency and accuracy and reduce labour costs.
3. Shipping & Receiving
After orders have been selected and packaged, they must then be shipped out to customers or stores via the most cost-effective route possible. At the same time, products must be received back from customers or stores who return them due to damage or faulty items.
The shipping/receiving process requires careful coordination between carriers, suppliers, staff and customers to ensure the accurate delivery of goods with minimal disruption.
4. Quality Control
Quality control is an important aspect of distribution centre operations as it helps ensure that all products meet required standards before being sent out to customers/stores.
Quality control processes may involve inspection (visual or using specialised equipment) and tests such as stress testing for electronic items or load testing for furniture to confirm their durability.
5. Transportation Planning & Logistics
Efficient transportation planning is critical in any successful distribution centre operation as it helps keep costs low while ensuring timely delivery of goods throughout their entire journey – from supplier location to customer doorstep/store shelf (and vice versa).
Transportation planning also entails analysing order volume patterns to match capacity with demand while also factoring in potential delays due to unforeseen circumstances such as weather conditions or traffic jams on highways.
The Five Benefits Modern Distribution Centres Offer E-commerce Stores
1. Increased Productivity
Modern distribution centres can improve productivity through features such as RFID tracking systems, automated pick & put-away solutions, and warehouse automation. This helps to maximise the efficiency of operations and reduce the amount of time required for tasks.
2. Automation
One of the main advantages of modern distribution centres is their ability to provide businesses with automated processes and tools to streamline their order fulfilment operations. Automated products such as robotic conveyor belts and automated sorting systems help to speed up processes and reduce manual labour costs.
3. Improved Inventory Management
With modern distribution centres, businesses can monitor their inventory in real-time and generate accurate data that can be used to make more informed decisions about product availability and stock levels. This helps to ensure that e-commerce stores have greater control over their inventory levels and reduce potential losses due to stock shortages or overstock.
4. Cost Savings
With automated systems, businesses can save on labour costs associated with manual tasks such as picking, packing or sorting orders. Furthermore, businesses may also be able to save on operational costs associated with supply chain management due to improved forecasting accuracy and inventory visibility offered by modern distribution centres.
5. Improved Customer Service
In addition to increased efficiency in order fulfilment, modern distribution centres also allow retailers to offer improved customer service through faster order processing times and more transparent delivery options from anywhere in the world, allowing customers more control over when they receive their orders.
How Bezos’ Distribution Centres Benefit E-commerce Stores
For growing e-commerce businesses, managing logistics can be a significant cost and time investment. Hiring staff, investing in technology and equipment, tracking inventory — these steps must come together before an order reaches the customer’s doorstep.
Yet despite this complexity and expense, outsourcing operations to a third-party logistics (3PL) often pays off, ensuring orders are shipped on time with accurate labelling. And with the power of Bezos.ai, your business can take advantage of competitive pricing when looking to outsource operations to a 3PL provider. Our services make it easy for companies to send out goods quickly and cost-efficiently, allowing you to maximise profits.
With Bezos, clients can tailor their product requirements and receive customisable solutions that cater perfectly to their needs. Our exceptional service guarantees every client a personalised experience where they feel heard and understood.
As a result, we have several positive reviews online and an overall 4.8-star average on Trustpilot.
Here is one of our recent five-star reviews:
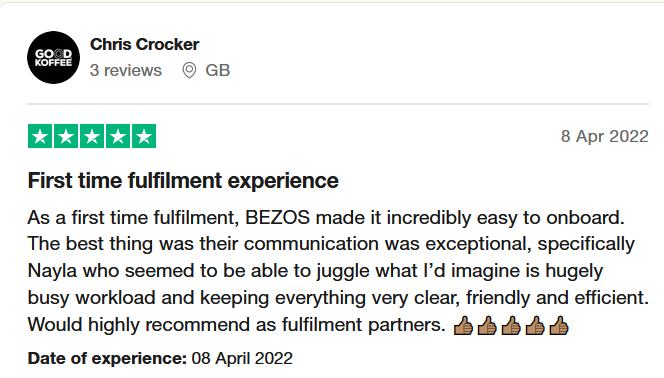
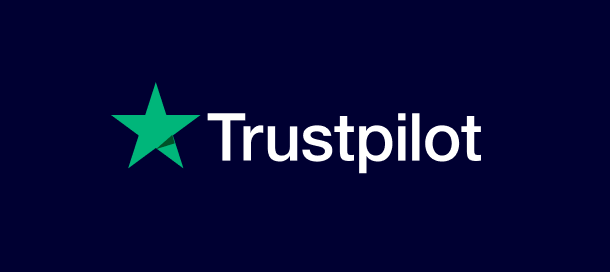
Through this excellent customer service, we allow brands to strengthen their customer relationships through refined fulfilment and delivery reliability. Our streamlined order journey removes the hassle of managing orders, enabling you to focus your resources on growing success.
Leverage this cutting-edge technology and customer service excellence for an efficient and cost-effective supply chain solution. Speak to an expert for a free quote, and expand your business today!
Schlussfolgerung
In conclusion, distribution centres provide a cornerstone for the supply chain, seamlessly connecting suppliers and customers by offering efficient storage solutions. Through these state-of-the-art warehouses, orders are fulfilled with speed, cost savings and value-added services, enabling businesses to meet their customers' needs in record time.
With Bezos, you can become a truly global business in no time. We offer an all-inclusive order journey solution so that you don't have to lift a finger – and with it comes improved customer service experiences and more efficient scaling abilities. Best of all is the budget-friendly price tag attached. Speak to an expert and see your company scale up like never before!
Häufig gestellte Fragen
What is an example of a distribution centre?
Distribution centres, such as perishable food and drink product warehouses, ensure goods go from point A to B quickly. From receiving shipments in the morning until they are distributed by day's end – efficient delivery is guaranteed. These shipments can be arranged internationally but be handled by local distribution centres to cut down on the time perishable items have to be in transit.
Why do companies use distribution centres?
Distribution centres play an essential role in any supply chain. Optimising the intake, processing, storage and distribution of goods saves money on temporary storage solutions, eliminates stockouts and ensures customers are satisfied with timely and complete orders.
What is another word for distribution centre?
Distribution centres are a powerful resource capable of serving multiple functions. Depending on the purpose of its operation, it can go by many different names – from DC as an abbreviated form, 3PL, fulfilment centre, warehouse and package handling centre, to a cross-dock facility. If you're looking for an efficient way to manage your business's operations and logistics needs, these versatile shipping site hubs may be just what you need.