What Is a 3PL Warehouse? Definition, Role, and Benefits
A growing online store faces many choices as it expands. Storing products in one’s garage or small leased space can work for a while. Yet as orders rise and customers expect faster delivery, handling every step of warehousing and logistics in-house becomes a heavy burden.
A third-party logistics (3PL) warehouse steps in where keeping up with demand, managing complex inventory flows and shipping orders efficiently become tricky. By handing over storage, picking, packing and shipping to a specialist, ecommerce brands and logistics teams can focus on other priorities, such as marketing, product development or customer service.
This article unpacks exactly what a 3PL warehouse is, how it operates, and why so many business owners and logistics managers choose to outsource storage and fulfilment. By the end, you’ll see why partnering with a 3PL warehouse may make sense if you want to optimise costs, scale faster and deliver a smoother experience to your customers.
Defining a 3PL Warehouse
A 3PL warehouse is a facility run by a third-party logistics provider. At its core, “3PL” stands for third-party logistics. Instead of keeping goods in your own storage facility or managing every step of order fulfilment internally, you outsource warehousing, inventory control, picking, packing, shipping and sometimes returns management to an external partner. The 3PL warehouse acts as your storage hub and dispatch point. It collects inventory from your suppliers or manufacturing sites, stores it according to agreed terms, and processes customer orders on your behalf.
What Is That “3PL” Versus “4PL”?
Choosing between a 3PL and a 4PL depends on how much of your supply chain you want to manage yourself versus handing off to a single partner. A 3PL handles core logistics tasks like storage and shipping, while a 4PL steps back to design, coordinate, and optimise every link in your network. The table below highlights the key differences.
If you want a deeper comparison between a third-party logistics provider and a fourth-party logistics partner, see our guide on 3PL vs 4PL.
How a 3PL Warehouse Operates
To understand why ecommerce brands trust 3PL warehouses, it helps to know how they run daily operations. Below is a simplified flow of steps once you have partnered with a 3PL provider. While each facility may vary in processes or technology, the core elements remain consistent.
Onboarding Inventory
When your products arrive at the 3PL warehouse, staff check and scan each item against your purchase orders. Any discrepancies—damaged cartons or missing items—get flagged immediately. The provider records SKUs, batch numbers or serial numbers to track inventory accurately. Some warehouses label or repackage goods to meet branding requirements or to standardise carton sizes.
Storage and Inventory Management
After inspection, products move into storage. Depending on volume and turnover, the 3PL may assign pick faces or bulk locations. A warehouse management system (WMS) tracks each pallet, carton or individual unit’s location. If you need “3pl warehouse locations in California,” your provider likely has fulfilment centres in major markets such as Los Angeles, San Diego or San Francisco. By placing inventory near key customer bases, you reduce transit times and shipping costs.
Order Receipt and Processing
When a customer places an order on your website, the order information flows directly into the 3PL’s WMS. Staff pick the required items from shelves, scan them to verify accuracy and move them to a packing station. The WMS often directs pickers on the most efficient route, boosting productivity. At packing stations, workers check item counts, add any promotional materials or instructions and pack the order in appropriate envelopes or boxes.
Shipping Label Creation
Shipping labels are generated automatically using the WMS or connected shipping software. Warehouse staff confirm the carrier selection—whether standard ground, expedited or same-day delivery—based on your configured rules. If you offer free returns or branded packaging, the 3PL incorporates those rules into fulfilment. Once labels are affixed, packages move to staging areas sorted by carrier.
Carrier Handover
Couriers pick up shipments at scheduled times. The warehouse coordinates daily or multiple driver stops per day to hand over parcels. Real-time data from scanned pickups feeds back into your order management system so you can alert customers that their order is en route and provide tracking links.
Returns Management
If a customer sends an item back, the 3PL processes the return: scanning the package, inspecting the contents, restocking acceptable items and updating inventory counts. Some warehouses can inspect, refurbish or repack returned items if they meet quality requirements. You avoid handling returns yourself, which frees up staff for other tasks.
Reporting and Analytics
Most 3PL warehouses offer dashboards summarising key metrics: pick accuracy, order cycle time, daily throughput, inbound receiving volumes and inventory ageing. These insights help you plan promotions, optimise stock levels and forecast demand. Access to real-time reports means you can respond to surges in orders, holiday volumes or unexpected supply chain disruptions.
For insights into ecommerce-focused storage options, explore ecom warehouse.
7 Core Services Offered by 3PL Warehouses
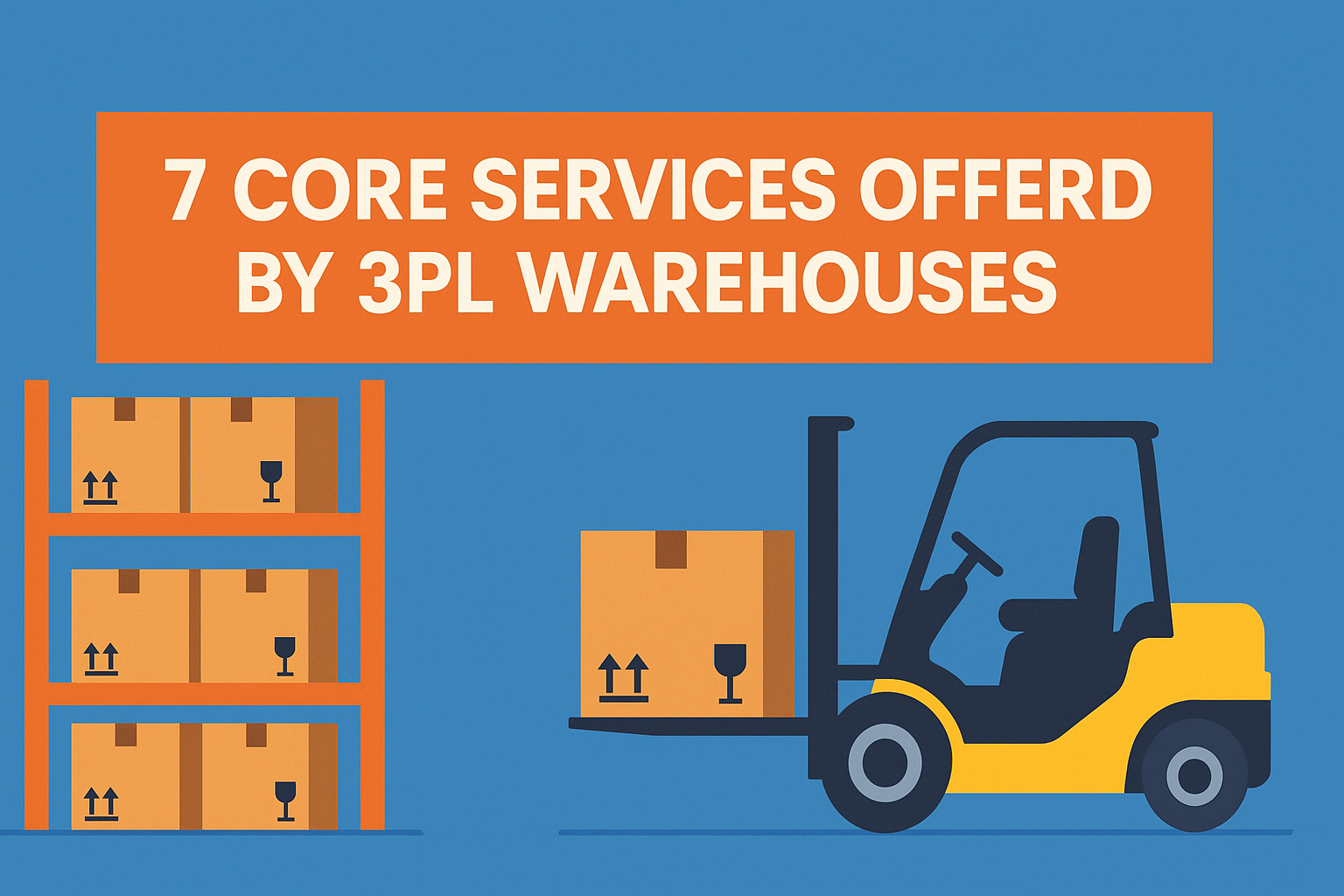
Alt text: A stylised graphic of a forklift lifting a box beside shelving stacked with boxes, under the heading “7 Core Services Offered by 3PL Warehouses.”
Not all 3PL providers offer the same suite of services. When evaluating options, it helps to know what common capabilities exist. Even if you only need basic storage and fulfilment today, selecting a provider with additional services can prove valuable as your business evolves.
1. Basic Warehousing and Storage
This is the foundation. The 3PL provides safe, secure space to store your products on pallets, shelves or in bulk bins. Depending on volume, you pay for allocated space or full pallets. Warehouses often offer flexible pricing tiers for short-term storage, seasonal peaks or long-term inventory. If you handle consumer electronics, apparel or beauty items, ensure the facility’s storage conditions match your requirements.
2. Order Fulfilment (Pick, Pack and Ship)
Warehousing without fulfilment still requires you to pick, pack and ship orders. A full-service 3PL handles all three. They use efficient picking routes, barcode scanners and packing stations to maintain high accuracy. Whether you ship small parcels or freight pallets, a 3PL can tailor processes to fit your needs. High-volume clients often receive dedicated picking lines or even shared conveyor belts to speed up processing.
3. Bonded 3PL Warehouse Services
A bonded warehouse holds imported goods on which duties and taxes have not yet been paid. You can delay payment until items leave the facility for domestic distribution. Bonded 3PL warehouse services benefit businesses importing products from overseas. You store inventory under customs bond, reduce cash flow pressure and fulfil orders without duties until items ship. If you sell to multiple countries or deal with high-value goods, bonding can simplify customs clearance and improve liquidity.
4. Temperature Controlled 3PL Warehouse
Some products require precise temperature ranges to remain viable—pharmaceuticals, perishable foods, cosmetics or certain chemicals. A temperature controlled 3PL warehouse provides refrigerated or frozen zones, often broken down further into controlled-room areas (e.g. 2–8°C, 15–25°C, – 18°C). Monitoring systems track temperature and humidity in real time, triggering alarms if conditions deviate. If you store seasonal fruit preserves or high-end skincare, you need a provider certified to handle temperature-sensitive goods.
5. Cross-Docking
With cross-docking, inbound shipments transfer directly to outbound carriers without intermediate storage. This approach speeds up order fulfilment and cuts handling costs. For instance, if you receive bulk pallets from a manufacturer destined for various retail stores, a cross-dock 3PL warehouse can sort and load cartons to different carriers or trucks on the same day. Cross-docking works well for high-volume, fast-moving goods with stable demand patterns.
6. Kitting and Assembly
Kitting means bundling multiple items—such as gift boxes, product bundles or subscription boxes—into a single SKU for shipping. Assembly can also involve minor light manufacturing steps, like attaching accessories, labelling or quality checks. A 3PL that offers kitting and assembly streamlines production. Instead of shipping raw components to you, suppliers send parts to the warehouse, where staff build kits per your instructions. You only pay labour costs in the warehouse rather than in your own facility.
7. Returns Management and Reverse Logistics
Handling returns often poses headaches for in-house teams. With reverse logistics services, the 3PL inspects returned items, decides if they can restock, refurbish or dispose of damaged goods, and update inventory accordingly. They can process refunds or replacements under your policies, reducing manual effort for your staff. If you have a generous return policy to drive sales, outsourcing returns to a 3PL removes a big chunk of administrative burden.
Types of 3PL Warehouses and Specialised Facilities
Not every 3PL warehouse looks the same. Depending on your product mix, regulatory environment and customer base, you may need specialised capabilities. Below are key facility types you might encounter:
To learn more about outsourcing fulfilment and how it ties into 3PL solutions, check out our page on fulfilment 3PL.
Advantages of Partnering with a 3PL Warehouse
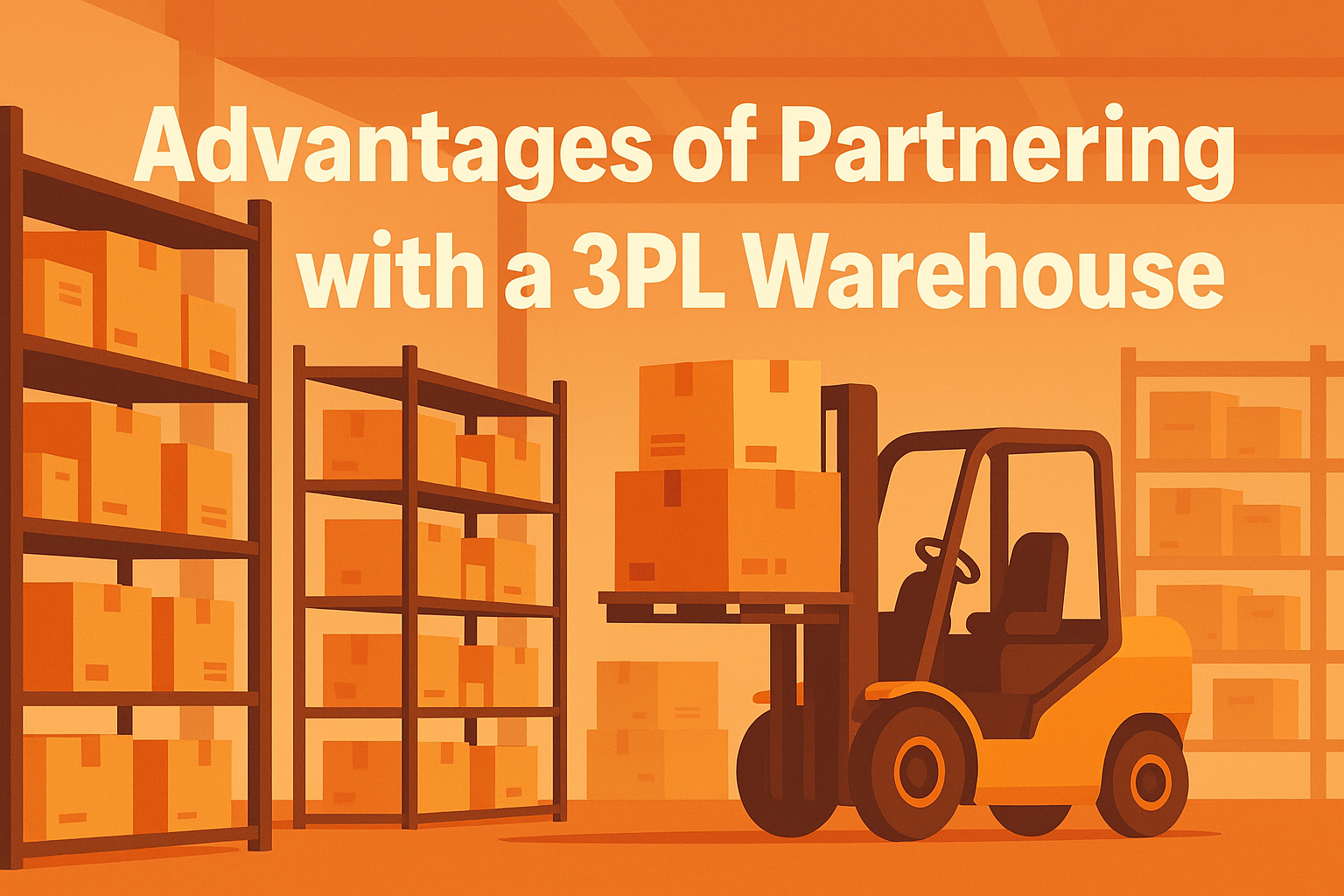
Alt text: A stylised warehouse scene with a forklift lifting a pallet of boxes beside tall shelving units.
Outsourcing to a 3PL warehouse yields several benefits that impact cost, performance and growth potential. Below, we highlight key advantages and explain why many ecommerce brands find this approach valuable.
Cost Savings and Predictable Expenses
Leasing a warehouse, hiring staff, maintaining equipment and investing in warehouse technology require substantial capital. When you partner with a 3PL, you only pay for the services you need: storage space, labour for picking and packing, and shipping fees. That model lets you convert fixed costs into variable costs.
Fees typically break down into:
- Storage Fees: Charged per pallet, per bin or by cubic metre, often billed monthly or weekly. Seasonal pricing may apply during peak periods, but you avoid paying rent on empty space when demand slows.
- Pick and Pack Fees: Charged per order, per item or per cart. You pay for each order processed rather than covering full-time salaries even when volumes dip.
- Shipping Fees: Passed through from carriers or negotiated rates. Some 3PLs offer discounted rates from major carriers due to volume.
- Value-Added Service Fees: For kitting, labelling, returns processing or other add-ons.
Because most costs align with volume, your expenses correlate directly to sales. That transparency helps with forecasting and budgeting. When you lease your own facility, you risk overpaying for unused space or under-resourcing labour when demand spikes. With a 3PL, you scale up or down without renegotiating leases or hiring temporary staff.
Faster Shipping and Improved Customer Experience
Speed matters. Customers often expect next-day or two-day delivery. By storing inventory at a 3PL warehouse near major urban centres—such as a 3PL warehouse location in California close to Los Angeles or Sacramento—you deliver products more quickly and at lower rates. A provider’s network of fulfilment centres places inventory strategically across regions. Instead of shipping coast to coast from a single location, you can split inventory across multiple warehouses, reducing transit distances by up to thousands of miles.
Fast, reliable shipping leads to happier customers, fewer complaints and higher repeat purchase rates. Returns also flow back to local warehouses, cutting down reverse transit times. In short, customers feel confident that orders will arrive on schedule. That trust builds brand loyalty, particularly in competitive product categories where delivery speed can be a deciding factor.
Évolutivité et flexibilité
When your sales surge—whether during a holiday flash sale, a viral promotion or a new product launch—handling high order volumes in a small in-house operation can prove daunting. A 3PL warehouse is structured to handle spikes, with flexible labour pools and scalable systems. They often run multiple shifts or bring in temporary staff during peak seasons. Because you do not own the workforce, the provider absorbs the burden of quickly expanding operations.
On the flip side, if orders dip unexpectedly, you do not carry payroll overhead for idle staff. You simply pay less for labour and storage. For startups or growing brands with fluctuating volumes, a 3PL offers flexibility without overextending resources.
Access to Advanced Technology
Modern 3PL warehouses use warehouse management systems (WMS) and software integrations that many small businesses struggle to afford. A robust WMS:
- Tracks inventory in real time across multiple locations
- Guides pickers along efficient routes
- Prints shipping labels automatically
- Monitors order accuracy and flags exceptions
- Provides analytics on order cycle times, inventory ageing and turnover
By plugging your ecommerce platform or ERP into the 3PL’s WMS, you gain up-to-date visibility into stock levels without building your own system. That visibility prevents overselling, keeps reorder points accurate and reduces stockouts. Many providers also offer dashboard views of key performance indicators, letting you monitor how well orders ship, average pick errors and regional demand patterns.
About Bezos
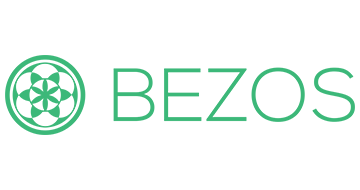
Alt text: The logo of Bezos.
Bezos specialises in tailored 3PL warehousing and fulfilment solutions for ecommerce businesses. Through seamless integrations and real-time inventory tracking, they simplify logistics so you can concentrate on growing your brand. Their strategically located warehouses ensure your products reach customers quickly and securely.
Ready to see how Bezos.ai can transform your fulfilment process? Request a Quote!
Conclusion
Partnering with a 3PL warehouse lets you hand off storage, picking, packing and shipping to experts, freeing up time and resources to focus on your core business. By tapping into a provider’s existing infrastructure, technology and strategic locations, you can deliver orders faster, reduce costs and scale more efficiently. Evaluate potential partners on factors such as location, integration capabilities and specialised services to ensure they align with your needs. With the right 3PL in place, you’ll enjoy smoother fulfilment operations and greater flexibility as your ecommerce venture grows.
FAQ
What does 3PL mean in warehousing?
3PL stands for third-party logistics. In warehousing, it refers to outsourcing storage, order fulfilment and related logistics tasks to an external provider, rather than handling these functions in-house.
What is that “3PL”?
“3PL” is simply shorthand for third-party logistics, meaning a specialised company manages distribution, shipping and inventory on your behalf. By partnering with a 3PL, you leverage their infrastructure, technology and labour to handle storage and fulfilment.
What is 3PL or 4PL?
A 3PL provider executes core logistics services—warehousing, picking, packing and shipping. A 4PL takes a broader role, coordinating multiple 3PLs, carriers and brokers to design and oversee your entire supply chain from end to end.
What is an example of a 3PL?
One well-known example is ShipBob, which offers ecommerce fulfilment centres handling storage, picking, packing and shipping for online brands. Another example is Amazon FBA, where sellers store inventory in Amazon’s warehouses and rely on Amazon to process and dispatch orders.